How to make a cutter for a mini tractor with your own hands from a car axle
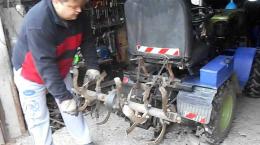
Previously, hand tools were used to cultivate the soil in the garden, local area or country house.
Today, many people have access to various agricultural machinery, so gardeners often use special equipment for cultivating the land - a small tractor with a milling cutter.
Many people ask how to save money and make a cutter for a mini tractor with your own hands?
This article will look at how to assemble such a phrase yourself with minimal experience and expense.
Content:
- Mini tractor cutter: what is it, why is it intended
- Design, operating features of the rototiller
- Description, characteristics of popular models
- How to make a homemade milling cutter from a bridge
- Do-it-yourself cutter for a mini tractor
- Homemade cutter for a mini tractor with your own hands from the Volga bridge
- How to replace a rototiller with a new one
- Useful tips and tricks
- Conclusion
Mini tractor cutter: what is it, why is it intended
This small mechanized cutting tool makes it possible to evenly cultivate the land during preparatory work for planting crops, sowing seeds or wintering.
Although the device is as simple as possible, it is multifunctional.
This unit simultaneously replaces three types of agricultural equipment: cultivator, plow and harrow.
The milling mechanism is quite simple; this design includes two wheels, a working shaft on which sharpened cutting plates are installed, a protective casing and a special gearbox.
This cutter, mounted on a mini tractor, is intended for the following types of soil cultivation:
- eliminating weeds and minimizing their growth;
- loosening the soil. The cutter qualitatively mixes the soil mixture with any types of fertilizers, both organic and mineral;
- soil structuring. It is possible on the equipment to select the degree of lumpiness of the earth;
- automation of many processes that a gardener or farmer performs when manually processing soil;
- reducing time and labor costs, increasing the efficiency of land cultivation.
The device is installed not on a regular tractor, but on a mini-tractor, thanks to which it makes it possible to cultivate plots and fields of not very large sizes.
A soil tiller makes it possible to simultaneously mix the soil, loosen it and remove all unwanted vegetation. This device can be used if there are no large stones or tree roots with a large diameter in the ground.
You will learn more about the mini tractor cutter by watching the video:
Design, operating features of the rototiller
Different models of cutters work on the same principle. The shaft with the cutting plates rotates, as a result of which the plates lift the top layer of fertile soil, the same thing happens when a person digs the soil with an ordinary shovel. The design of the rototiller makes it possible to speed up this process several times and make it mechanized.
To set the shaft in motion, the diesel engine of the minitractor runs, which transmits mechanical force to a special gearbox mounted on the cutter body. Through the gearbox, the shaft with knives begins to rotate, and by adjusting the power of the gearbox, a person speeds up or slows down the rotation of the shaft.
The support wheels adjust the depth to which the cutter blades will go deeper into the ground. And the frame of this device is necessary to connect the equipment to the mini tractor. Thanks to the protective metal casing, which is located on top of the knives and shaft, the working mechanisms are protected from dirt, dust and other contaminants.
Description, characteristics of popular models
Today the market offers many models of rototillers installed on small tractors.
Here is a list of the most popular models and their characteristics:
- FR-00010. It is manufactured in Minsk, although this milling cutter is intended for small MTZ tractors, this model can be adapted to any equipment of this class. The device is capable of working on heavy and light soil; work on inclined surfaces up to 10 degrees is allowed. This unit makes it possible to adjust the width of the cultivated soil, from 44 to 61 cm. The milling cutter loosens the soil to a depth of 12 centimeters. The productivity of this equipment is a maximum of 0.2 ha/h, the weight of the device is 47 kg;
- FNM-1. This Belarusian equipment requires a shaft rotation speed of at least 357 rpm. In one pass, it processes from 44 to 60 cm of soil, going 80 millimeters into the soil. The weight of the device is about 50 kg, in 1 hour it makes it possible to process up to 0.2 hectares, this figure will vary depending on the hardness of the cultivated land;
- GQN-125.This device has a wide grip; in order for it to work successfully, a tractor with a power of 24-30 l/s is required. This cutter captures 125 cm of soil in one pass. The knives go 20 cm deep into the soil. The cutter shaft rotates at a speed of 180-250 rpm; to develop this speed, the power take-off shaft must rotate at a speed of 540 to 730 rpm. The weight of this equipment is 210 kg.
How to make a homemade milling cutter from a bridge
The bridge from any passenger car is used as a basis.
All unnecessary elements that will not be used in the cutter are cut off from the bridge. The bridge is installed on a metal frame, which is manually welded from metal pipes or channels; the frame should be located on two wheels so that the bridge is at a height of 30-70 centimeters from the ground surface.
The length of the bridge is shortened to the required size.
To secure the milling shaft, it is necessary to make homemade metal jaws from iron; the thickness of the metal used is from 8 to 12 millimeters.
To make the cutter shaft, a thick-walled pipe is taken, its diameter is about 50-60 millimeters. Several segments, from 5 to 10 pieces, are welded to the milling shaft, onto the ends of which knives, for example, “crow’s feet,” are welded.
On the shaft and on the bridge, 2 sprockets are installed on both sides, the number of teeth of which ranges from 18 to 28, two chains are put on the sprockets on both sides of the bridge and the shaft, the pitch of the chain must correspond to the pitch of the teeth on the sprockets.
The cutter shaft is fixed to the bridge using a metal plate about 10 mm thick. A protective metal casing is placed over the sprockets with chains. The chains must be coated with grease.
Do-it-yourself cutter for a mini tractor
Since the soil mill is a simple design, it can be made independently, at home.
To assemble this device, you will need the following tools:
- welding;
- drill;
- Angle Grinder;
- spanners;
- bolts and nuts.
The first step is to produce a metal frame. To make it, you will need either an iron pipe or a metal channel, the diameter of the pipe must be at least 40 mm, and the thickness of the channel must be 5 millimeters or more.
The selected material is cut into 4 pieces, the resulting parts are welded together using a welding machine. The width of the resulting frame can be from 50 to 150 cm, depending on the power of the small tractor.
When creating a metal frame, the places where the support wheels will be installed are provided. They must be mounted in such a way that it is possible to adjust the distance of the cutter frame to the ground.
After securing the frame and installing the wheels, the shaft is secured to the frame at a distance of 30-50 centimeters from the ground, depending on the length of the milling knives.
To transmit traction force, the metal shaft is connected through a gearbox to the tractor power take-off shaft. The shaft must be secured to the welded frame through bearings and bushings.
Knives are made from strips of metal, the thickness of which is 10-12 millimeters. Experts recommend using only high-strength tool steel for the manufacture of metal knives, because they will experience the main load. Depending on the width of the shaft, use a suitable number of knives.
For example, for a device with a width of 120 cm, four elements are taken on which three legs are installed. Be sure to bend each leg at the end at an angle of 70-90 degrees; these bends will loosen the soil. The knives are secured to the shaft through threaded connections. All structural elements that will rub against each other must be lubricated with oil or grease.
We invite you to watch an interesting video about how to make a cutter for a mini tractor with your own hands:
Homemade cutter for a mini tractor with your own hands from the Volga bridge
Using a bridge from a Volga car, a soil tiller is made for a small tractor, for example, a T-40. The width of the milling installation is 180 cm. First, a frame is made from metal corners or squares, the size of the frame is 180x60 centimeters, the base of the cutter will be installed on this frame.
The frame is welded on a flat plane so that there are no distortions, after which the washer and bearing are removed from the Volga bridge. The bridge is cut with a grinder to the length of the frame; it is important to cut at a right angle.
The bridge is installed on top of the frame, and the cutting part of the cutter with knives is mounted at the bottom of the frame, the knives are secured to a metal pipe-axis, which is installed through bearings and secured to the frame using a plate.
How to replace a rototiller with a new one
Depending on the type of rototiller, its elements are replaced with new ones.
You must act in the following sequence:
- the metal casing is removed from the shaft;
- The shaft mounted on the mini tractor and the rototiller shaft are connected to the transmission transmission shaft. It is important to ensure that the axle pin is securely locked;
- a small tractor is rolled up as close to the cutter as possible;
- lift the connecting links located at the bottom of the device;
- The clamp plug is inserted into the connector. It is important for those connecting links that are located in the lower part to be securely connected to each other using a locking pin;
- the upper links are connected, they are also connected using a pin.
They disassemble the soil tiller and replace it with a new one according to the same scheme, only they do everything in the reverse order.
Useful tips and tricks
To extend the life of the milling unit, it is important to follow some recommendations from specialists and equipment manufacturers. Structurally, these units are very similar to each other, so the tips given below are relevant for any model of rototiller.
Here are the main, most important recommendations:
- Before starting to operate the equipment, it is important to check how reliable the fasteners and connecting elements of the structure are. If the need arises, it is important to adjust the connections.
- The gearbox contains a lubricant - oil, it is important to regularly check the amount of this oil; if the level is below the permissible level, be sure to add lubricant.
- If the rototiller is being used for the first time, it is important to carry out preliminary preparatory work. This preparation consists of running in for one to two hours, while the cutter should experience minimal load. If the run-in was successful, the main work begins.
- Before using the device, it is important to carefully and slowly read the instructions provided by the equipment manufacturer. After this, install the knives and operate the cutter strictly in accordance with the instructions.
- After each use of the device, it is important to clean the unit of any contaminants, including plants, dust and dirt.
Before the winter period or at other times when the device will not be used for a long period, the articulated coupling is removed from it. And the cutting elements are lubricated with grease or oil so that they do not rust.
If any breakdown occurs, when a certain part of the equipment fails, they purchase a replacement part in a specialized store or on an online resource, of which there are quite a lot now.
Cutting elements often break, especially if you have to loosen dense, hard soil. Gears and bearings also fail, especially during intensive use of the unit. Buying components is not difficult, the main thing is to know exactly the model of the rototiller.
Let's watch a video about testing a self-slow cutter:
Conclusion
A person who knows how to use plumbing tools and welding well can make a rotary cutter for a mini tractor with their own hands.
Before you start making a device, it is important to impartially assess your capabilities.
If you do not have the necessary knowledge and skills, it is better to entrust the manufacturing process to a specialist or purchase a ready-made cutter from a specialized store.